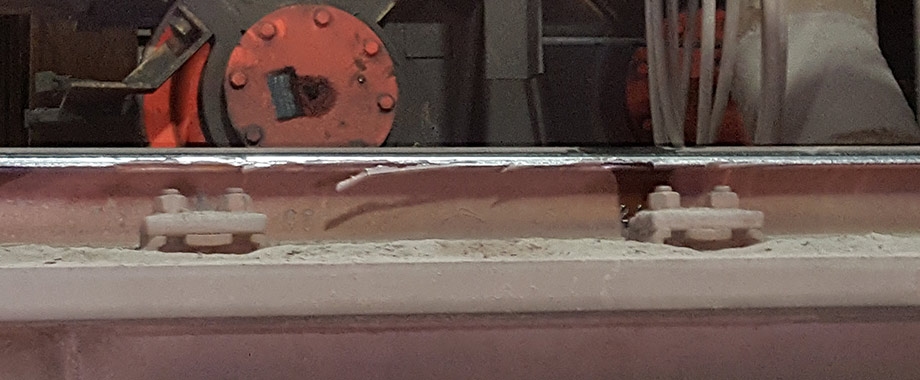
Crane Rail Alignment Survey
SDC has successfully performed crane rail alignment surveys in steel mill buildings for over 20 years. The old practice of performing an optical survey has been largely replaced with laser and laser scanning techniques. Crane rail alignment surveys using optics or lasers require a lock-out of the crane runway. Movement from cranes operating in adjacent runways also needs to be eliminated or controlled to maintain a straight baseline. Laser scanning does not require a runway lock-out but cost and accuracy are issues.
SDC recommends the use of lasers (not laser scanners) which are faster and data can be downloaded to quickly generate an AutoCAD drawing. However, SDC uses a jig to mount the prism to accurately measure the inside edge of the crane rail or crane girder. The use of pole mounted prisms will not result in obtaining the accuracy necessary to meet CMMA requirements.
Laser scanning is used to measure the edge of the crane rail. However, crane rails do not have vertical machined surfaces and may be worn as shown in the image at the top of the page. SDC has not experienced good alignment results from laser scanning. Some Maintenance Managers have reverted back to optics to shoot a crane runway. Our survey procedure is briefly described below:
Field Measurements
Repeatability is very important when crane runways are surveyed. SDC not only punch marks base lines on each side of the runway, we punch mark other column locations to help ironworkers install new or move crane rails. It is also helpful to have permanent monuments at grade level in all buildings with crane runways for repeatability. Operation and Maintenance need to schedule the time to install safety cables and provide access to the crane runway when crane rail alignment is an issue.
EOT Crane Survey
SDC performs surveys to determine the end truck alignment, wheel alignment, and wheel gauge. The crane runway punch marks are used to tie the crane and crane runway surveys together.
- SDC recommends taking measurements from the base line to the equalizing pins, each end of each end truck and three (3) points on each wheel.
- A 90 degree angle can be turned from the runway base line to determine if the crane is square. Distances from the perpendicular line from the base line need to be taken at the wheels and end trucks. The crane can also be quickly checked for square by taking diagonal measurements from the four (4) permanent squaring marks on the end ties.
Crane Rail/Girder Survey
SDC will establish survey baselines that will be used to measure the offsets to the crane rails, crane girders, and column flanges. SDC will take the measurements off the baseline at the ends and center of each crane girder. Many crane girders are bowed near mid-span due to torsional stresses. A photograph of a bowed 112 foot long crane girder can be seen in Photograph #1 here. Crane rail measurements will be taken off the baseline to the crane rail at the same locations. The relative elevations of the crane girders will be shot at each building column.
CMMA Requirements
- Crane Span
The nominal crane span can vary (+/-) 3/16″ for a 50 foot long crane. The variance is increased to (+/-) 1/4″ for a 50-100 ft. long crane span and (+/-) 3/8″ for a crane span longer than 100 feet. - Crane Rail Straightness
The nominal crane rail span can vary (+/-) 3/8″ with a maximum rate of change of 1/4″ in 20′-0″. - Crane Rail Elevation
The nominal crane rail elevation can vary (+/-) 3/8″ with a maximum rate of change of 1/4″ in 20′-0″ along a column line. - Rail-To-Rail Elevation
The nominal crane rail elevation across the bay can vary (+/-) 3/16″ with a maximum rate of change of 1/4″ in 20′-0″ along a column line for a 50 foot long crane. The variance is increased to (+/-) 1/4″ for a 50-100 ft. long crane span and (+/-) 3/8″ for a crane longer than 100 feet. Note: The girder depths are to be (+/-) 1/32”. For adjacent girders this means a tolerance of (+/-) 1/64” for each for each girder with a variable thickness sole plate. SDC does not follow this requirement and allows a 1/16” height differential between girders for crane rail bearing. This requires proper field measurements to achieve.
AIST Technical Report 13 Requirements
- Crane Span
The nominal crane span can vary (+/-) 1/4″ regardless of the crane length between rails. - Crane Rail Straightness
The horizontal misalignment of crane rails shall not exceed 1/4″ in 50′-0″ with a maximum of ½” total deviation from the theoretical location. - Crane Rail Elevation
The nominal crane rail elevation shall not exceed 1/4″ in 50′-0″ with a maximum of ½” total deviation from the theoretical location. - Crane Rail Misalignment With Crane Girder Web
Crane rails should be centered on the crane girder webs whenever possible. In no case shall the eccentricity be greater the three-fourths of the girder web thickness.
Crane Rail Alignment Drawings
SDC generates AutoCAD drawings showing the results of the crane/rail survey along with a recommended crane rail realignment or girder shimming as required. It is our experience that it is nearly impossible to maintain the CMMS and AIST Tech 13 Requirements due to various, permanent building movements.
SDC will recommend a best fit crane rail alignment with the crane girder centerline. Crane rails will be offset as much as ¼” in 25 feet. SDC has moved crane rails as much as 3 “ off girder centerline. There are currently no guidelines to help Engineering or Maintenance Departments deal with over/under gauge of the crane girders. SDC performs a full crane girder torsional analysis (including warping normal and shear stresses) to determine the girder stress state when the rails must be offset from the girder centerlines. Our crane girder designs include a rail offset of L/400.
Wheel/Rail Interference Study
SDC can use the crane and crane runway survey data to perform an interference study between the crane wheels and over/under gauged crane rails. This study is used to determine if crane rails need to be relocated off the crane girder centerlines.
Crane Rail Shims
SDC does not recommend use of shims to level a crane rail. We normally shim the column base plate or column cap plate. AIST Technical Report 13 shimming requirements are not practical and can cost hundreds of thousands of dollars. SDC recommends having a rail-to-rail elevation tolerance of 1/16” between adjacent crane girders. This is a tolerance of +/- 1/32” which is the best we can do. SDC has experienced no crane rail breaks due to a knife edge at the end of a crane girder using our 1/16” tolerance.